3D printing is revolutionizing the way we make things. It allows for the manufacture of products that would be impossible or at least extremely difficult using traditional subtractive manufacturing techniques.
The most common method is Fused Deposition Modeling, where a plastic filament is melted and deposited layer by layer, building up the desired product. Click https://www.by3design.com/ to learn more.
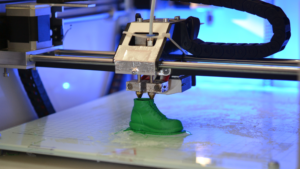
When you’re a designer, it’s important to have a way to validate your ideas. Traditional prototyping methods like mock-ups and wireframes are time-consuming to build and expensive. But with 3D printing, you can make a prototype in hours that looks and feels like the final product. This allows you to test your design and quickly make changes.
This process is known as rapid prototyping or iterative design. It involves creating a model of your product or process, testing it with users and stakeholders, and adjusting the design accordingly. This iterative process is critical to the success of your project. It minimizes the risk of investing in a product that doesn’t meet user needs or expectations and reduces product development costs.
To create a 3D model, you need a design that’s created with a computer program. This software is often referred to as CAD, or computer-aided design, and it can be purchased or found online. The design is then converted into a file format that can be printed by a 3D printer, such as STL (standard triangle language). The resolution of this file should be optimized so the printer can produce the desired results.
Once the file is ready to print, a filament is passed through the printer and used to construct the object. The result is a physical representation of your design that can be used for iterative testing with users or to share with engineers for production planning purposes.
A physical prototype is often preferred for user testing than a digital visualization, as it leaves less to the imagination. This helps your team to better understand the look and feel of a design, and allows them to compare concepts side by side.
High-fidelity prototypes are also useful for communicating production intent to tooling specialists, and they can be used to communicate the intended functionality of a product to potential investors or sales representatives. Additionally, they can help designers to identify any design, size, or shape issues early on, before making costly commitments in the production process.
Additive Manufacturing
Additive manufacturing (AM) is a process that turns virtual solid models into physical objects using layer-by-layer fabrication techniques. The process was once primarily used for prototyping but has rapidly been adapted to production applications as well.
AM technologies allow the construction of complex and geometrically precise products that are otherwise impossible to fabricate by traditional methods. These products can be made with a range of materials including polymers, metals and ceramics and are based on the geometry suggested by the solid modeling side of computer-aided design (CAD). They have opened up new possibilities for product development and manufacturing.
For example, it is possible to create internal architectures that could not be designed and built in the past because of manufacturing limitations. These architectures can also influence the mechanical properties of the finished component. It is also possible to print components with a high degree of accuracy, which can lead to substantial reductions in cost and weight.
Unlike conventional manufacturing, which uses molds to shape and hollow out solid blocks of material, 3D printing creates physical objects by building up layers of material. The process is referred to as additive because it adds layers of material one on top of another rather than cutting or milling the object out of a solid block.
A virtual model of the desired object can be made by a variety of tools, such as CAD software that can create precise drawings and technical illustrations or a 3D scanner that takes pictures of the object from different angles. The model is then broken down into many layers by a process called slicing, which prepares it for printing.
The slicing is then converted to a series of instructions for the printer, which builds up the object layer by layer until it is complete. It is a much faster and more accurate process than making the same product with conventional tools.
Industrial-scale AM is increasingly becoming a viable alternative to other manufacturing processes for mass production of complex parts in industries such as aerospace, automotive, mobility and consumer goods. Companies such as EOS have pioneered the technology and are enabling its use in demanding industrial applications, providing a powerful tool for competitive advantage.
Data-Driven Manufacturing
A manufacturing enterprise must commit to data-driven decision-making if it wants to stay competitive. Embracing this approach allows leaders to improve operational efficiency, reduce costs, improve quality, and support sustainability goals. The key to achieving this goal is to analyze data that is available through your systems. This data can be gathered through your shop floor equipment, operators and the supply chain, among other sources. This data is essential to making informed decisions and can be used to develop a product roadmap.
A manufacturer can also use this data to create new products and streamline existing production processes. It can also identify potential challenges and take proactive measures to address them. Data-driven manufacturing is a key element in driving success in today’s fast-paced business landscape.
The first step in becoming a data-driven manufacturer is to invest in the right technology. This includes implementing the best software and hardware to collect, analyze, connect and manage your data. The right software can automate processes, reduce human error and allow for better strategic planning. It can also help you make more effective operational and maintenance decisions, as well as streamline supply chain management.
Manufacturing data is growing rapidly with over 1000 EB (billion bytes) collected in 2015. Data can range from explicit values like material properties and process temperatures to implicit ones such as customer preferences and supply chain resources. The challenge is to find the most valuable information and apply it to your operations in a way that drives real-time results.
3D printing is an advanced manufacturing technique that uses computer-controlled printers to build up parts layer by layer, unlike traditional methods that cut away material to form the final product. It has several advantages over other traditional manufacturing techniques such as machining, casting and forming. The primary benefit of 3D printing is its ability to produce complex geometries that would be impossible to produce using other methods, such as casting or machining.
In addition, it offers many other benefits for manufacturers including speed and efficiency, reduced cost, and the ability to make complex shapes with varying degrees of complexity. It is also environmentally friendly, as it requires fewer materials than other traditional manufacturing methods and can reuse plastics once the part has been used.
Sustainability
Throughout the years, alarm about the impact of human activities on the environment has steadily risen. This is particularly true of the manufacturing sector, which is known for its huge consumption of natural resources and the resulting pollution. However, 3D printing and other additive processes have the potential to greatly reduce these effects.
For example, 3D printing allows manufacturers to reduce the quantity of raw materials needed for production, saving them money and eliminating waste. They can also prioritize local resources, reducing the carbon footprint of transportation and energy costs, and they can cut down on storage and handling costs. Finally, since spare parts can be produced on an as-needed basis, fewer materials are needed to produce a given number of products. This reduces inventory and overall production costs while promoting circularity.
3D printing can also help reduce industrial pollution. 19% of the world’s greenhouse gas emissions are related to manufacturing, but 3D printing can significantly lower these numbers by limiting the amount of materials needed. Furthermore, the technology can be used to create biodegradable plastics. These are much safer for the environment than conventional petroleum-based plastics.
Another way that 3D printing can help improve sustainability is by allowing companies to use recycled materials in their productions. Many companies offer this option, and it is possible to find eco-friendly 3D printer filaments that are made from wood, recycled plastics, or cellulose. However, it is important to remember that even eco-friendly materials may contain trace amounts of harmful chemicals.
A number of new construction methods and innovations are being developed for the building industry, with 3D printing playing a major role in this revolution. For example, a company called Reef Arabia is using 3D printing to create marine-grade sandstone coral to plant in the ocean and regenerate depleted coral reefs. This company is just one of many that are using 3D printing to improve efficiency, cost-effectiveness, and sustainability in building and construction. This is the kind of innovation that can truly transform the building and construction sectors and change how people live and work around the world.